Five-Axis Milling Precision for Large Customized Wind Turbine Parts
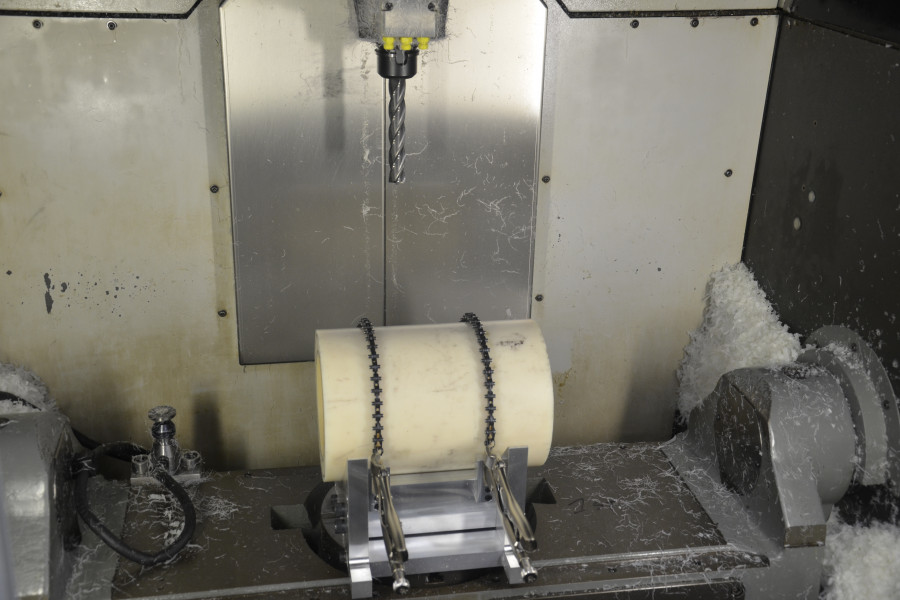
In an era in which most companies have fewer resources and even less time to get their products and services to market, Marten Machining helps companies grow. How? By solving high precision manufacturing challenges with customized designs and prototypes manufactured to submicron quality tolerances with very little lead-time.
The latest example of this is Marten Machining’s work with a manufacturer of wind turbines. The company’s challenge was, in a fashion, its success. With their wind turbines in high demand, they simply didn’t have the time or personnel to solve one of their challenges — they needed a customized part to secure the cables within the wind turbine towers. And they needed to deliver those parts across the U.S. in just four weeks.
So they turned to Marten Machining. Notes Dave Marten, “The part they needed manufactured was actually a large part — and its design required high precision five-axis milling. They didn’t have the machines, the people or the time to manufacture that part. We did.” Marten adds, “Because the part was so large, we actually had to create two custom fixtures to hold the part within the five-axis milling machine, and we had to reload the part several times in order to complete the high precision milling. Because we specialize in high precision manufacturing, we had the knowledge, personnel and time to quickly design, manufacture, test and deliver the product. We were able to solve their problem for them — and that allowed them to keep manufacturing their wind turbines.”
With the custom fixtures in place, Marten Machining was able to cut down on the frequency of part loadings and shorten the lead-time. Concludes Marten, “We had the machine they needed and we came up with a way to use that machine in the best way possible with customized tooling. It was a complete success.”