Always Room for Improvement — Marten Machining Utilizes Rapid, Low-Volume Process Change Precision Machining to Improve Client Efficiencies
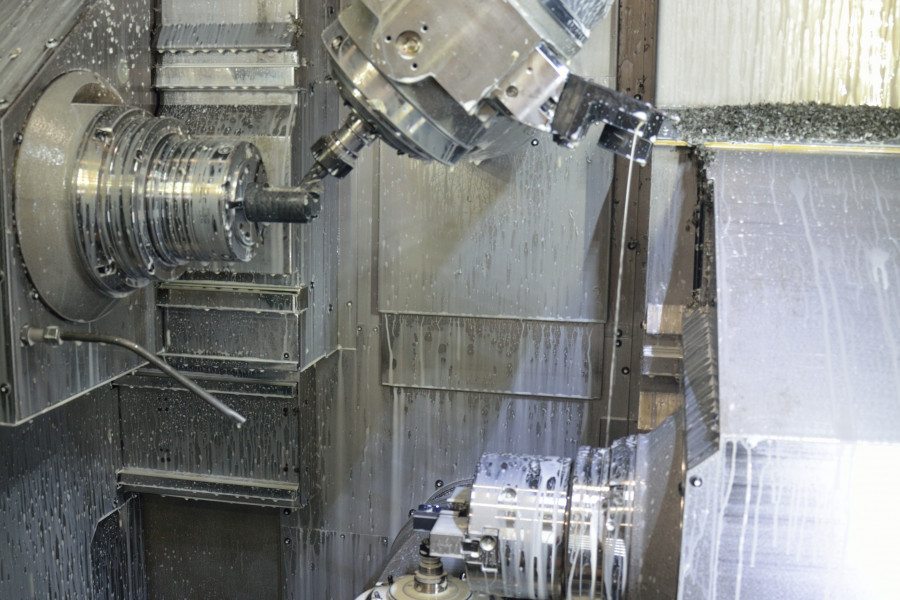
In the manufacturing industry, precision tooling, fixtures and specialized parts are evolving —and that’s a good thing because it allows manufacturers to create customized products for their clients. At the same time, this evolution can place additional burdens on manufacturers who lack the resources to design, manufacture and test the very parts that are critical to their manufacturing process. That’s where Marten Machining comes in.
Marten Machining works with manufacturers that often produce small-volume, customized parts with very little lead-time. Marten Machining recently revamped its high precision manufacturing process for a client who produced customized modular packaging machines.
Marten Machining manufactured specialized grippers on behalf of the client. The original process, designed by Marten Machining, utilized rectangular plastic strips that were placed into a milling machine set up to perform five variable operations. Five pieces of plastic were placed into five fixtures of the milling machine, with each piece milled in succession. Every four-and-a-half minutes, when a piece was completed, the unfinished pieces would be advanced in assembly-line style and a new piece of plastic was inserted into the first fixture. This process required constant personal attention during a 10-hour shift.
Marten Machining knew they could improve that process, thus optimizing their clients’ efficiencies for a project with only a four-week lead-time. Enter the Index R200 65 mm bar capacity mill-turn multitasking machine. The R200 completes multiple high precision operations in one cycle, requires limited operator interaction and has two 65mm turning spindles and two 18,000 rpm milling spindles capable of simultaneously milling and turning on both the main and counter spindles.
With the R200 in place, Marten Machining was able to utilize rounded pieces of plastic — improving materials efficiencies. The R200 mill-turn machine also works on two pieces at once —turning, milling and transferring the pieces from one spindle to the other while simultaneously working on the back and front sides of the pieces. Now, all of the high precision work is done in one cycle with the completed piece dropped onto a conveyor belt by a robotic arm. The parts can now be manufactured in 18-hour shifts without the need for constant personal oversight, improving lead-time and production efficiencies.
The R200 is critical to manufacturers of small-volume parts as well because it’s easy for Marten Machining to make 150 of one item and 200 of another because there’s no extra set up time and very little switch over time.